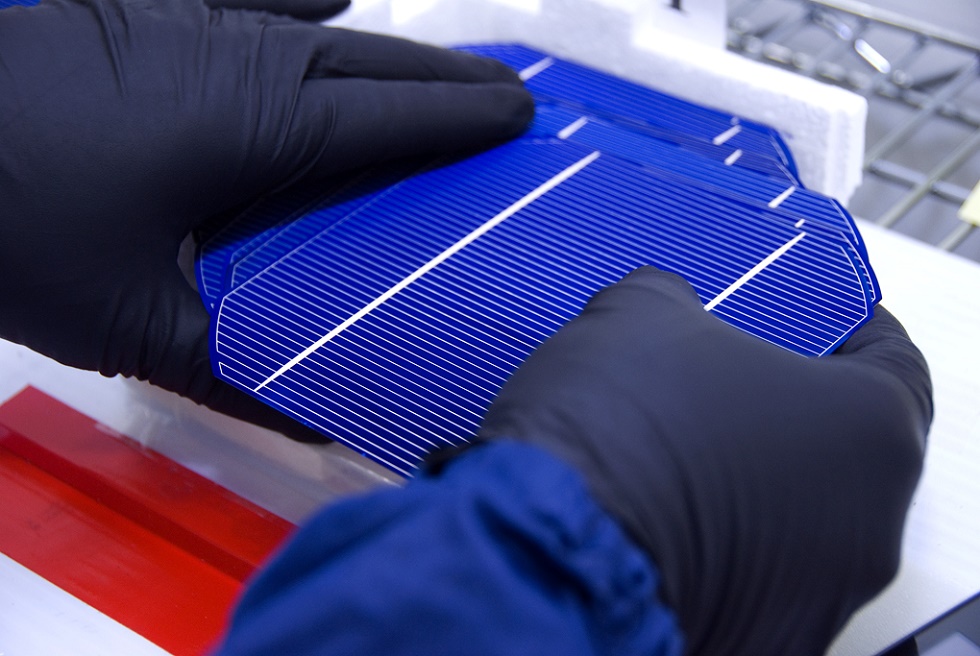
A new method developed by German researchers saves half of the silicon used in the production of solar cells.
Solar cells are built by thin sheets of silicon that converts sunlight into electricity. But in the silicon factories today, more than 50 percent of the silicon is wasted.
Silicon Waste
Researchers at the Fraunhofer Institute in Germany aimed to reduce this waste using a new process that cuts the usage of silicon in production by half. And at the same time, it reduces energy consumption by 80 percent.
Silicon wafers are manufactured in a process of dissolving a piece of impure silicon in acid, mixed with hydrogen gas. This gas mixture is then transformed to pure polysilicon.
But since polysilicon is not used in solar cells, the material is then broken into pieces, then melted and converted into several large blocks of crystalline silicon. These are then split into smaller pieces.
New Production Method
The process developed by the German scientists starts the same way, but skips the whole detour via polysilicon and instead uses a method called chemical vapor deposition. By which the silicon-containing mixture flows past a substrate that covers its surface. Thus building a silicon wafer one atomic layer at a time.
The method excludes the need to cut the silicon into shapes, a process in which much material might be lost. Another advantage is that it is possible to create wafers considerably thinner than today’s solar cells. And the thinner the solar cells, the cheaper.
All in all, this makes for a wafer cost that is halved, while the cost of finished solar modules is reduced by 20 percent. The company Nexwafe now aims to implement the technology with a goal to start mass production late 2017.
_____________
Low-cost wafers for solar cells
__________________________