They rotate objects to supersonic speeds and slingshot them into space. Now Spinlaunch has conducted the first test with the accelerator concept.
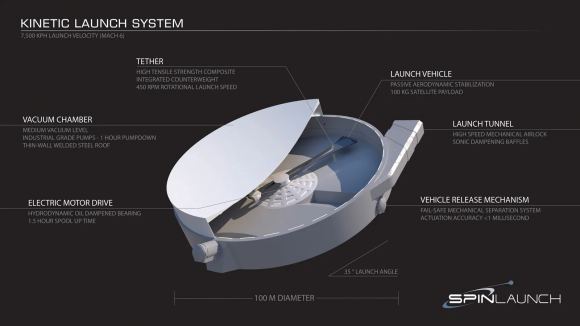
There are many ideas on how to launch objects into space without using conventional rockets. One company that has come a long way is the American company Spinlaunch.
They have just recently carried out a first test of the company’s electric accelerator. Their Suborbital Accelerator fired off an object that reached supersonic speeds. More tests are expected in 2022, and the hope is to be able to serve customers as early as 2024.
The company began developing the concept in 2015. The idea is pretty simple in theory. Using a mass accelerator, the company’s kinetic energy space launch system would be enough to throw objects into space with enormous acceleration.
The concept feels ripped right from the classic age of science fiction, is based around a vacuum-sealed centrifuge that spins an unpowered projectile at several times the speed of sound before releasing it, hurling it into the upper atmosphere, and ultimately into orbit. It’s sort of like the Olympic hammer-throw event, but with satellites instead of metal balls.
The first test flight of a prototype — a so-called suborbital accelerator called Orbital Launch System (OLS) took place at Spaceport America in New Mexico on October 22. The test was a crucial stepping stone towards creating the company’s proposed OLS, which will conduct regular payload launches soon.
In 2018, Universe Today reported on how SpinLaunch and its CEO Jonathan Yaney had come out of “stealth mode” and sought Series A funding. By 2019, the company broke ground on its test facility at Spaceport America, followed by constructing the Suborbital Accelerator. Measuring 33 meters in diameter (108 ft) in diameter, the Suborbital Accelerator is the world’s tallest instrument of its kind and costs about $38 million to build.
However, the system is only a one-third-scale model of the OLS system that is currently under development and relies on the same components. Like the OLS, the Suborbital Accelerator uses a vacuum-sealed centrifuge to spin a rocket and then catapult it to space at up to 8,000 km/h (5,000 mph). The rotational kinetic energy comes from ground-based electricity provided by solar and wind (which would eliminate the carbon footprint of rocket launches).
The system uses a vacuum chamber within which a rotating arm brings a projectile up to very high speed without any drag penalty, before hurling it into the atmosphere “in less than a millisecond,” according to the company, as a port opens for a fraction of a second to release the projectile. A counterbalance spins in the opposite direction to prevent the system from becoming unbalanced. The vacuum seal stays in place until the projectile breaks through a membrane at the top of the launch tube.
Within the next eight months, SpinLaunch plans to conduct about 30 more tests of its suborbital accelerator in New Mexico — which was only putting 20% of its total power behind this first test flight — before building the larger orbital accelerator capable of putting satellites into orbit.
SpinLaunch expects its orbital system will be able to deliver about 440 pounds (200 kg) of payload into orbit per launch — the weight of two small satellites. This payload will be a tiny fraction of what most rocket launches carry — SpaceX’s Falcon 9, for instance, can carry over 50,000 pounds (22,800 kg) to low-earth orbit. However, SpinLaunch says its approach will be 10 times cheaper and require 4 times less fuel than what’s currently used to put payloads of its size into orbit. It also produces “zero emissions in the most critical layers of the atmosphere.”
The main problem is the enormous acceleration and the potential stress it would pose to the often very complex objects that are to be launched into space. The company has tested its high-g reaction wheels — which included a 12m (~40 foot) variant – with multiple types of payload and reported that even “unmodified smartphones, action cameras, and telescope lenses have survived without damage.” At the same time, the company is also working on ways to “ruggedize” satellites for the high-g conditions associated with kinetic launches. As they state on their website:
“SpinLaunch is engineering a variety of efficient satellite chassis, which require no more than a 10% increase in mass compared to those designed for the traditional launch environment. Satellite structures optimized for the high-g environment are readily analyzed with finite element modeling with predictions that closely match real-world testing, allowing for rapid iteration and development. The net result is a family of structural components that are ready-to-use with little to no impact to mass or cost.”
Perhaps we will soon see a future where massive disc-like structures dot the coast and act as our primary means of space access.